Unleashing Precision and Innovation in Metal Fabrication for Plastic Injection Tooling
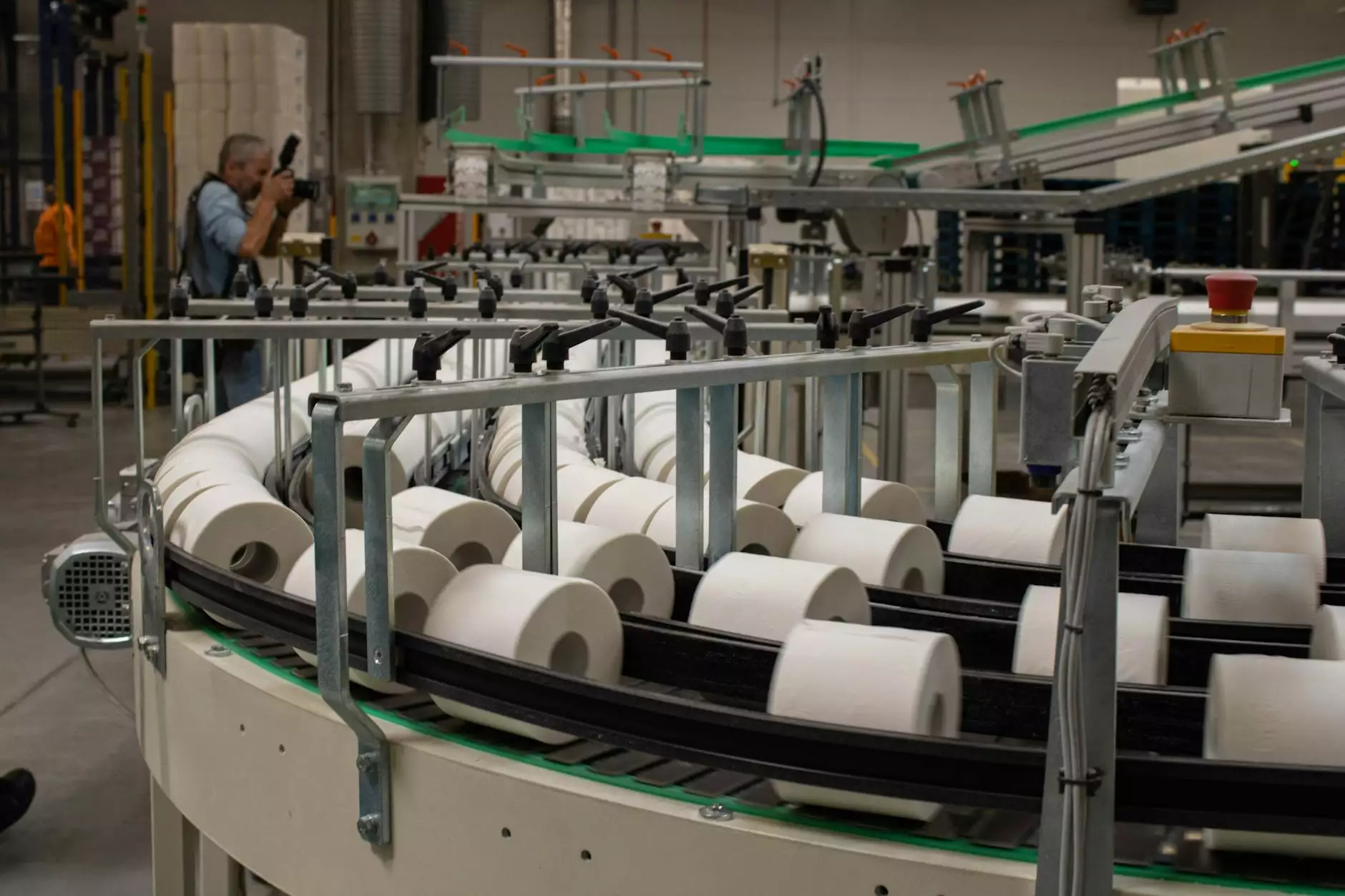
DeepMould.net stands at the forefront of the manufacturing industry, offering unparalleled expertise as a dedicated metal fabricator with a specialized focus on plastic injection tooling. Our mission is to deliver high-precision, robust, and innovative solutions that empower manufacturers to dominate their markets and achieve operational excellence.
The Critical Role of Metal Fabrication in Plastic Injection Molding
In the realm of modern manufacturing, metal fabrication serves as the backbone of high-performance plastic injection tooling. The quality, durability, and precision of the tooling directly impact the final product's quality, production efficiency, and cost-effectiveness.
Our expertise at DeepMould.net encompasses designing and fabricating tooling components that meet the stringent demands of injection molding processes. From complex cavities to intricate core inserts, our advanced fabrication techniques ensure each component performs flawlessly under rigorous production conditions.
Why Choose DeepMould.net for Metal Fabrication in Plastic Injection Tooling?
- Unmatched Precision: Leveraging state-of-the-art CNC machining, wire EDM, and laser cutting, we produce tooling components with micron-level accuracy, ensuring perfect fit and function.
- Material Mastery: We utilize an extensive range of high-grade metals, including hardened steel, stainless steel, aluminum, and specialized alloys, selected based on specific application requirements.
- Innovative Design Support: Our engineering team collaborates closely with clients to optimize tool design, enhancing durability, cycle times, and product quality.
- Rigorous Quality Control: Every fabrication undergoes comprehensive inspection procedures to validate dimensional accuracy and mechanical integrity before delivery.
- End-to-End Service: From initial concept to final production, we offer complete support including prototyping, testing, and maintenance of injection molds.
The Art and Science of Plastic Injection Tooling
Creating high-quality plastic injection tooling demands a perfect blend of engineering prowess and craftsmanship. Our process at DeepMould.net emphasizes meticulous attention to detail at every stage.
Design Optimization for Superior Injection Molds
Effective plastic injection tooling begins with intelligent design. We employ advanced CAD software and simulation tools to analyze flow, cooling, and ejection, minimizing defects and cycle times. Our designs focus on:
- Efficient Venting: Avoids trapped air and burn marks.
- Uniform Wall Thickness: Ensures consistent molding and reduces warping.
- Simplified Ejection Systems: Enhances mold lifespan and reduces cycle time.
- Durable Core and Cavity Structures: Withstanding high-volume production and maintaining precision over millions of cycles.
Fabrication Techniques Tailored for Plastic Injection Tools
Our fabrication processes are tailored to meet the demanding standards of injection mold manufacturing, including:
- CNC Machining: For complex geometries with tight tolerances.
- Wire and Sink EDM: For intricate cavity and core detail not achievable through conventional machining.
- Heat Treatment: To enhance wear resistance and structural integrity of tooling components.
- Surface Finishing: Precisely polishing mold surfaces to achieve desired surface finishes and aesthetic requirements.
Key Benefits of Our Plastic Injection Tooling
Partnering with DeepMould.net ensures numerous advantages that empower your manufacturing operations:
- Lower Production Costs: Durable, precise tooling reduces cycle times and minimizes scrap.
- Enhanced Product Quality: Consistent molds produce parts with tight tolerances and superior surface finishes.
- Accelerated Time-to-Market: Rapid turnaround times from design to production enable quick market entry.
- Flexibility in Production: Customizable tooling solutions accommodate a wide range of product designs and materials.
- Sustainable Manufacturing: Accurate tooling reduces waste, energy consumption, and overall environmental impact.
Enduring Value with Custom Metal Fabricated Plastic Injection Tooling
Our emphasis on quality, innovation, and customer satisfaction ensures that your investment in plastic injection tooling delivers long-term value. We understand that each project is unique, and we tailor our manufacturing processes accordingly.
By choosing DeepMould.net as your metal fabricator partner, you benefit from a combination of advanced manufacturing technology, experienced engineers, and a commitment to excellence that guarantees reliable, precise, and durable tooling solutions for your manufacturing needs.
Future Trends in Metal Fabrication and Plastic Injection Molding
The industry is continuously evolving with emerging technologies such as additive manufacturing, smart tooling, and automated fabrication systems. Our company stays ahead of these trends by integrating cutting-edge methods to improve efficiency and quality.
Some key future-oriented developments include:
- 3D Printing for Rapid Prototyping: Accelerating initial design validation and reducing lead times.
- Smart Molds with Embedded Sensors: Providing real-time data for predictive maintenance and process optimization.
- Automation and AI in Fabrication: Enhancing precision and reducing labor costs supply chain-wide.
- Sustainable Material Use: Committing to eco-friendly metals and reducing waste in the fabrication process.
Partner with DeepMould.net for Superior Metal Fabrication and Plastic Injection Tooling
DeepMould.net offers a comprehensive suite of solutions designed to meet the rigorous demands of modern manufacturing. Our expertise in metal fabrication and plastic injection tooling ensures that our clients stay competitive, innovative, and ahead of the curve.
Contact us today to discover how our custom fabrication techniques can elevate your production capabilities and lead your business into a new era of manufacturing excellence.