The Transformative Power of RA to RMS in Metal Fabrication
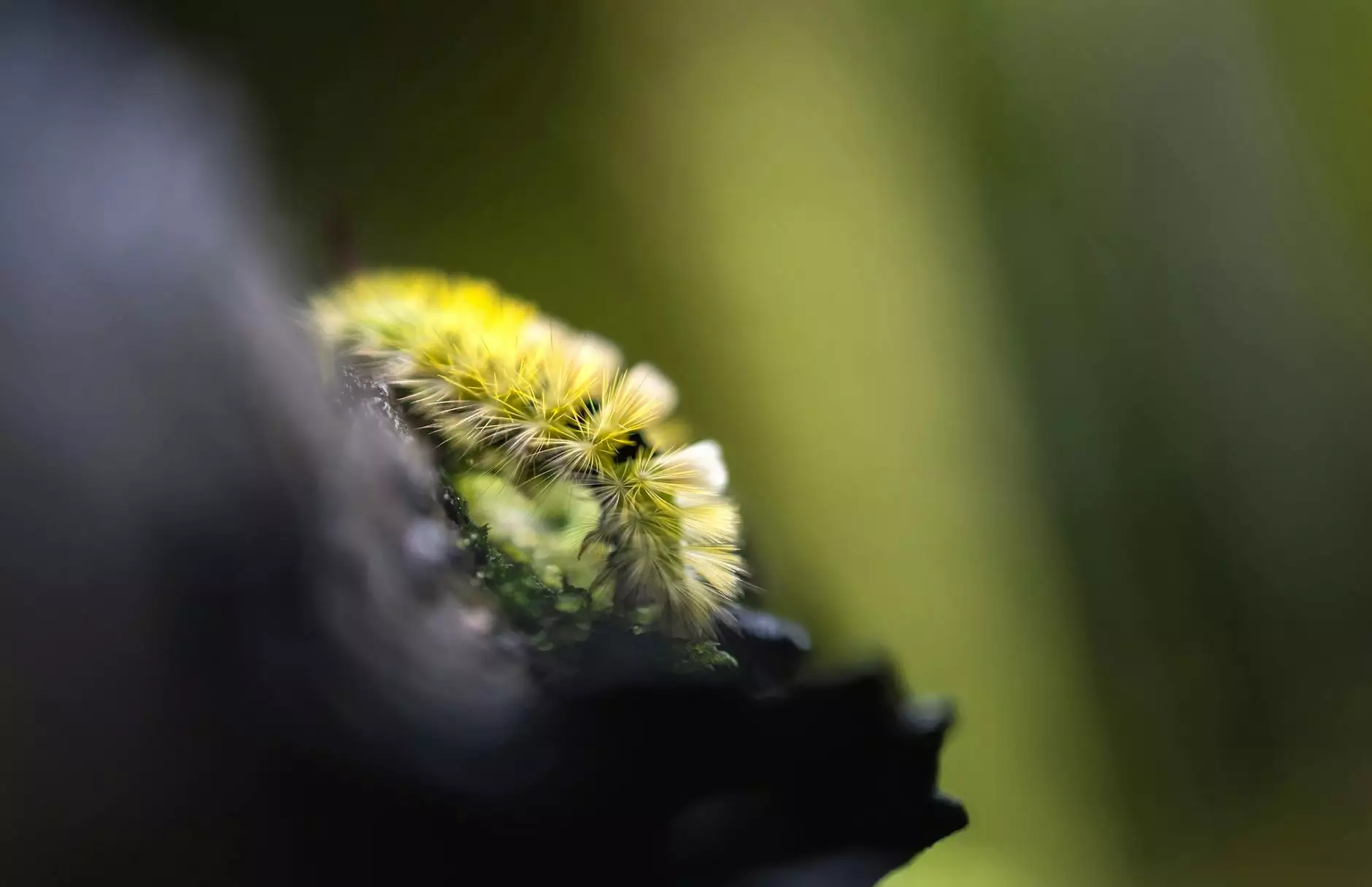
The world of metal fabrication is intricate and defined by various technical processes. One such fascinating topic is the transformation from RA to RMS. This transition is essential not just in the realm of electrical engineering but also within numerous applications in manufacturing and metalworking. In this extensive article, we shall delve deep into what RA and RMS represent, their significance, and how understanding this transformation can positively impact the industry.
Understanding RA and RMS
Before we explore the transformation from RA to RMS, it is imperative to understand what these terms signify.
What is RA?
RA, or Average Roughness, is a measurement used primarily to characterize the texture of a surface. It quantifies the average deviation of the surface profile from a mean line over a specified length. In metal fabrication, RA is pivotal as it determines the surface finish of the product. A lower RA value indicates a smoother surface, while a higher value signifies roughness. This metric is crucial for determining the performance characteristics of a component throughout its lifespan.
What is RMS?
On the other hand, RMS, which stands for Root Mean Square, is a statistical measure that reflects the amount of variation or dispersion in a set of values. It effectively captures the average magnitude of varying quantities and is extensively used in signal processing, particularly in analyzing or simulating AC voltage or current signals. In manufacturing, measuring RMS values can provide insights into the overall energy content or 'power' of the signal being analyzed.
The Significance of RA to RMS Transformation
As we transition from the simplistic measurement of RA to the more complex RMS, it becomes crucial to understand why this transformation matters.
Importance in Metal Fabrication
Metal fabricators must pay close attention to surface finishes. The RA to RMS conversion helps in defining the precision and quality of the finished product. A surface that is both smooth (low RA) and energetically stable (analyzed through RMS) often leads to better performance in real-world applications. This transformation is not merely academic; it directly impacts the operational efficiency of the final product.
Quality Assurance and Control
Incorporating RMS measurements in the quality control process allows engineers to ensure more consistent surface finishes and overall better performance. In applications that require high precision—such as aerospace, automotive, and medical industries—the RA to RMS conversion provides a more comprehensive understanding of surface characteristics and performance. This ultimately leads to reduced wear and tear and enhanced durability of components.
How to Measure RA and RMS
To effectively utilize the conversion from RA to RMS, one must know how to measure both values accurately.
Measuring RA
RA is typically measured using a contact stylus or laser scanners. A stylus runs along the surface, recording the vertical deviations, from which the average value is computed. This straightforward method is widely used due to its simplicity and effectiveness.
Measuring RMS
RMS is calculated using the formula:
RMS = √(1/n ∑(x_i²)), where x_i represents each individual measurement and n is the total number of measurements.
This mathematical approach evaluates all deviations and portrays a fuller picture of energy fluctuations, which is particularly useful in fluctuating signal environments.
The Conversion Formula: From RA to RMS
An essential aspect of this discussion is how to effectively convert RA values to RMS values. The general relationship can be approximated by:
RMS = RA x 0.7937
This formula indicates that the RMS value is roughly 79.37% of the RA value for many surface profiles. Understanding this conversion is critical, as it allows businesses to predict and control surface performance more accurately.
Applications of RA to RMS Transformation in Metal Fabrication
The practical applications of understanding the transformation between RA to RMS stretch across numerous industries. Here are some notable applications:
Aerospace Industry
In aerospace, component reliability is non-negotiable. Designers lean on RA and RMS data to ensure surfaces will endure extreme conditions. For instance, turbine blades require a surface of low roughness and high stability to minimize wear and maximize efficiency. Even small deviations can have significant consequences in terms of longevity and safety.
Automotive Sector
Similarly, the automotive industry capitalizes on this transformation. Engine components, gear systems, and braking systems must exhibit high-performance metrics to ensure reliability and safety. A thorough understanding of surface finishes and their impact on mechanical interactions helps manufacturers produce vehicles that operate more efficiently while minimizing emissions.
Medical Devices
In the realm of medical devices, the surface finish can drastically affect biocompatibility and functionality. Products ranging from surgical instruments to implants must be designed with an understanding of how surface textures influence biological interactions. Here, the RA to RMS transformation is a critical factor in quality assurance protocols.
Challenges and Considerations in RA to RMS Measurement
While the transformation from RA to RMS presents numerous benefits, it is not without its challenges. Understanding these challenges is key for professionals in metal fabrication.
Measurement Accuracy
Sensitivity of the measuring instruments is crucial. Any variance can lead to erroneous conclusions about surface quality. Thus, it's essential to implement regular calibration of devices and select the appropriate instruments for varying surfaces.
Surface Anomalies
Every surface has unique characteristics, and the presence of anomalies like scratches or pits can distort measurements. It's vital to train staff in recognizing these imperfections and factoring them into any calculations involving RA and RMS.
Data Interpretation
Translating RA and RMS data into actionable insights can be complex. Engineers must be adept at understanding the implications of these values, integrating them into design considerations, and assessing performance outputs in real-world scenarios.
Conclusion: The Future of Metal Fabrication with RA to RMS Insights
As industries evolve and demand for precision increases, the significance of understanding the RA to RMS transformation will only grow. By harnessing this knowledge, businesses like deepmould.net can enhance their production processes, ensuring the highest quality for their clientele.
A mastery of surface finishes and their impact through effective RA and RMS analysis not only guarantees performance but also fosters innovation, leading to superior products and processes. In a competitive landscape, the organizations that effectively manage these transformations will surely pave the way for future success in metal fabrication.
Call to Action
If you are interested in elevating your understanding of metal fabrication processes and leveraging the RA to RMS transformation in your business, consider reaching out to deepmould.net. Together, we can forge a path towards innovation and excellence in metal fabrication.